La méthode DMAIC (Définir, Mesurer, Analyser, Innover, Contrôler) est un cadre structurant issu du Lean Six Sigma, largement adopté dans les démarches d’amélioration continue.
Elle se distingue par son orientation résultats, son exigence de rigueur méthodologique et sa capacité à générer des gains mesurables.
Dans cet article, nous présentons une étude de cas réelle menée dans une entreprise manufacturière de taille moyenne, opérant dans le secteur de la transformation des matériaux, où l’application du DMAIC a permis de réduire les rebuts de production de plus de 40 % en six mois.
1. Contexte et problématique initiale
L’organisation cible est une entreprise canadienne spécialisée dans la fabrication de pièces métalliques destinées à l’industrie automobile.
Malgré un équipement moderne et une expertise technique reconnue, elle fait face à un taux de rebut avoisinant les 9 % sur l’une de ses lignes phares : la ligne de découpe/emboutissage.
Ce niveau est bien supérieur au standard sectoriel (< 4 %), il cause :
- Des pertes financières directes (matière première, temps machine, main-d’œuvre),
- Une baisse de la capacité productive réelle,
- Une dégradation de l’engagement des opérateurs,
- Une tension avec les clients due à des livraisons retardées.
La direction a décidé de piloter un projet DMAIC, confié à une équipe multifonctionnelle avec un Black Belt en amélioration continue comme chef de projet.
2. Définir (Define)
Objectif du projet
Réduire le taux de rebut sur la ligne d’emboutissage de 9 % à 4 % en six mois.
Livrables de cette phase
- Charte de projet DMAIC : validée par la direction, elle formalise l’objectif, l’équipe, les indicateurs clés (KPI), le périmètre et les hypothèses de départ.
- Voice of the Customer (VOC) : une série d’entretiens avec les clients internes (logistique, maintenance, qualité) et externes (constructeurs automobiles) révèle une exigence forte sur la stabilité des livraisons et la qualité sans reprise.
- SIPOC (Suppliers, Inputs, Process, Outputs, Customers) : cartographie macro du processus pour cadrer le périmètre.
Résultat clé
La problématique est reformulée clairement : « Comment réduire le taux de rebuts dus à des défauts de pli et de déchirure lors du processus d’emboutissage, sans altérer les cadences actuelles ? »
3. Mesurer (Measure)
Objectif
Évaluer la performance actuelle du processus et valider la mesure du problème à l’aide de données fiables.
Activités réalisées
- Collecte de données historiques sur 12 mois : taux de rebuts, type de défauts, opérateurs, lots de matière, température ambiante, cadence machine.
- Validation des systèmes de mesure (MSA) : audit du processus de mesure via des Gage R&R (Repeatability & Reproducibility).
Résultat : le système de mesure est fiable à 92 % — suffisant pour mener l’analyse.
- Process Mapping détaillée : diagramme de flux illustrant chaque étape de la ligne, avec insertion de points de contrôle qualité.
Résultats
- Le taux de rebut moyen est de 8,9 %, avec des pics à 12,5 % en certaines périodes.
- Les défauts récurrents sont concentrés sur trois types : pliage prématuré, déchirure en bord de pièce, et défaut de centrage.
- Le phénomène est particulièrement critique lors du changement de lot de matière première.
4. Analyser (Analyze)
Objectif
Identifier les causes racines expliquant les variations observées dans les rebuts.
Méthodologie utilisée
- Pareto : 80 % des défauts sont concentrés sur 3 types de défauts et sur 2 des 4 presses.
- Ishikawa (diagramme de causes à effets) : brainstorming structuré autour de 6M (Main d’œuvre, Méthode, Machine, Milieu, Matière, Mesure).
- Analyse statistique multivariée :
- ANOVA pour identifier les effets significatifs des paramètres de production.
- Régression logistique : modélisation de la probabilité de rebut en fonction de la pression, température, vitesse et dureté matière.
Découvertes clés
- Variation de la matière première : un fournisseur en particulier montre une variabilité de dureté (HRB 68 à 73) supérieure au standard. Les lots les plus durs augmentent de 30 % la probabilité de déchirure.
- Réglages de presse non standardisés : les opérateurs règlent la pression et la vitesse selon leur ressenti.
- Formation insuffisante : les nouveaux opérateurs n’ont pas de référentiel documenté de bon réglage.
- Planification de la production : la séquence des commandes n’est pas optimisée selon les caractéristiques des lots matière.
5. Innover/Améliorer (Improve)
Solutions proposées (et testées via PDCA)
- Mise en place d’un mode opératoire standard (SOP) avec réglages préconisés selon la dureté matière.
- Changement partiel de fournisseur pour les matières premières hors spécifications.
- Plan de formation spécifique pour les opérateurs avec validation des compétences (matrice de polyvalence).
- Check-list de début de lot : inspection matière, réglage machine, validation premier article.
- Simulation de séquence de production : regroupement des commandes par caractéristiques mécaniques pour limiter les sauts de réglages.
Pilotage et test
Un plan pilote a été déployé sur deux semaines, sur une seule presse. Les indicateurs suivants ont été mesurés :
- Taux de rebut : passé de 9,1 % à 5,2 %.
- Temps de réglage : réduit de 18 %.
- Engagement opérateur : hausse du score à 8,4/10 dans le baromètre interne.
Après validation, le plan a été généralisé.
6. Contrôler (Control)
Objectif
S’assurer de la pérennité des gains obtenus et installer une culture de contrôle visuel et d’amélioration continue.
Actions mises en place
- KPI visuels sur Gemba : affichage du taux de rebut en temps réel par presse.
- Audit mensuel de conformité aux SOP.
- Rituels de brief quotidien pour partager les écarts et renforcer la culture qualité.
- Amélioration continue intégrée au management visuel : suggestion d’idées Kaizen en lien avec les défauts résiduels.
- Procédure de réaction rapide (Andon) en cas de pic de rebuts.
Résultats finaux après 6 mois
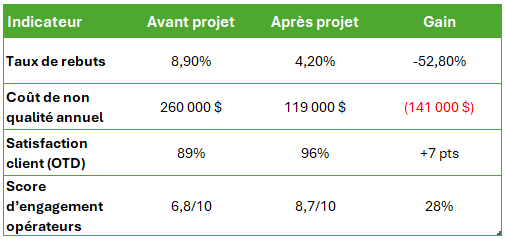
Enseignements clés
- La rigueur méthodologique du DMAIC est un levier puissant pour structurer les projets d’amélioration et mobiliser les parties prenantes.
- La mesure est un prérequis absolu : sans données fiables, les décisions deviennent spéculatives.
- L’analyse multivariée permet d’objectiver les causes et de dépasser les perceptions ou habitudes opérationnelles.
- La phase Improve ne doit pas se limiter à des actions techniques : la formation, les rituels et la gestion du changement sont tout aussi cruciaux.
- Le pilotage de la pérennité passe par l’ancrage dans la routine de gestion, non par la seule documentation.
Conclusion
Cette étude de cas DMAIC montre comment une approche structurée, outillée et participative peut transformer un problème chronique en levier de performance durable.
Le DMAIC n’est pas seulement une méthode : c’est un état d’esprit orienté vers la maîtrise, l’amélioration continue et l’apprentissage collectif.
© 2025 Centre de l’Excellence Opérationnelle. Performer pour plus de valeur. Tous droits réservés.